Overcoming challenges in the manufacturing
industry through technology
New improvements to the Odoo ERP systems used by the cement manufacturing
industry, can save manufacturers at least 2-3 million dollars in installation and
maintenance throughout a 10-year system
life cycle
investment.
ERP for Cement Industry
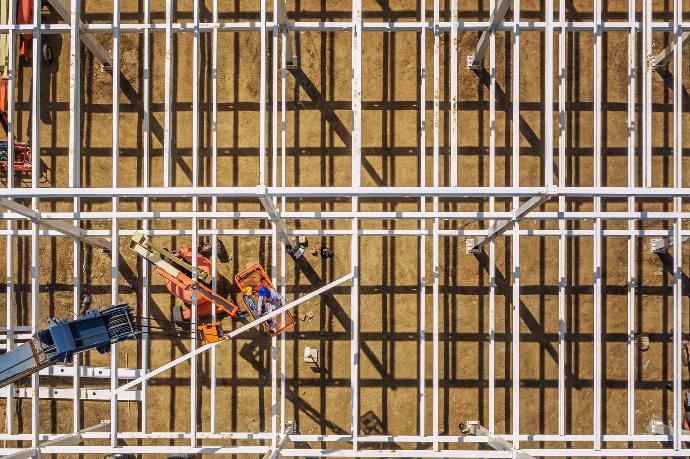
Typically many complex systems are used to manage the core processes. They include:
1
Extraction of raw materials
2
Crushing and grinding of raw material
Mixing and Preheating
Heating Final Grinding
Storage in silos
Best ERP for Cement Industry
Odoo ERP enables a new flexible way of modifying the use of the ERP to execute all the back office functions within a platform that is user-friendly and easily scalable.
By streamlining the processes and optimising the way each department interacts with the operations in the company, synergies across departments from sales through to finance to manufacturing can be closely monitored and enhanced to ensure the products sold to customers maximise the market conditions and gives the company a nimble execution across all functions.
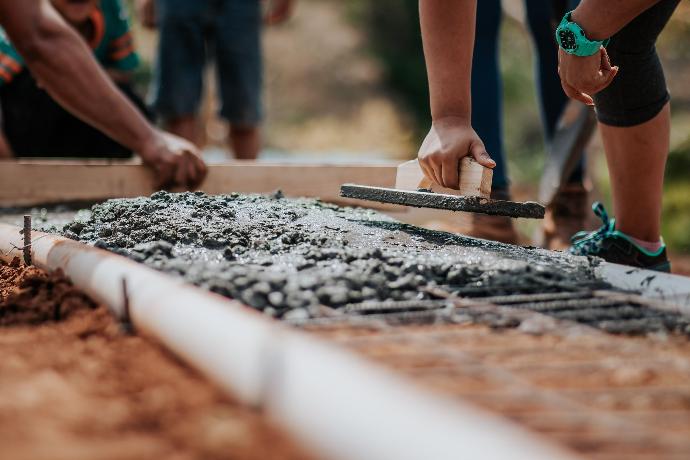
Overcoming Challenges in the Manufacturing Industry Through Technology
New improvements to the Odoo ERP systems used by the cement manufacturing industry can save manufacturers at least 2-3 million dollars in installation and maintenance throughout a 10-year system life cycle investment. Due to the saas nature of the system, the usual costs associated with legacy systems of requiring huge investments in managing physical systems and personnel on-site alongside ensuring 24-7 efficiencies have been negated with the corresponding savings.
Odoo ERP is at the forefront of embracing new features such as digital signature and an integrated document management system that offers a compelling proposition for manufacturing companies.
Cement manufacturing systems will continue to evolve like all areas as the drive to focus on innovative and cost-reducing systems continues to give real-time analytics and information that can feed into the business decision making.
A typical manufacturing plant has over 200 different types of machinery with a multitude of sensors and electrical systems that need to be at optimal capacity at all times to reduce loss of downtime. In cement manufacturing, the control system is more complex. Despite that, the systems are evolving daily. One of such possible evolution may be the entry of new digital-driven technology in the form of a system that provides bulk order fulfilment without human intervention.
A customer arrives at a facility to pick up an order of bulk cement in an articulated truck. By parking the truck under a silo and inserting a key fob that controls the systems, cement is disbursed to the correct quantity ordered without any human contact.
The savings in terms of manpower and being able to run the facility at a lower cost are drivers to adopt such automated systems which lead to an increase in the financial efficiency of a facility.